The presentation ”Application of LWD Acoustic Dispersive Data Processing for High-Quality Shear Slowness Logs in Slow Formations” will be given by Taher Kortam, from Halliburton.
Abstract:
For conventional acoustic monopole sources in a logging-while-drilling (LWD) or wireline environment, shear slowness logs can be hard to obtain, particularly in slow formations where direct refracted shear-wave arrivals are often absent. For LWD dipole sources, formation flexural waves are often coupled with the lowest order of tool flexural waves, so the flexural mode does not approach shear wave slowness at low frequencies. A dispersion correction is required to extract shear slowness from LWD dipole data. Instead, quadrupole firing, which generates screw waves, is considered the best LWD excitation mode for shear measurement. A fundamental feature of screw waves in an LWD environment is that their non-leaky cutoff frequency slowness is the formation shear slowness. However, slowness data near the cutoff frequency of LWD screw waves are often influenced by noise or the presence of other modes because of low excitation amplitude.
To overcome these LWD data processing challenges, we propose a data-driven processing method that uses all useful dispersion responses of existing modes in the frequency domain. The process first generates a differential phase frequency-slowness coherence map and extracts the slowness dispersion vs. frequency. Then, it computes the slowness density log, referring to the intensity of the dispersion response along the slowness axis. Next, an edge-detection method is applied to capture the edge of the first peak associated with shear slowness on the slowness density map. To refine the shear slowness answer, this initial estimate of shear slowness serves as the input to another algorithm that minimizes the misfit between the screw slowness vector and a simplified screw dispersion model. The simplified screw dispersion model consists of a pre-computed base library of theoretical screw dispersion curves and two data-driven parameters. The two data-driven parameters are used by the measured data to stretch the base dispersion model in the frequency and slowness axis, respectively, to account for errors generated by alteration, anisotropy or other parameters that are not included in the forward modeling. The method can also be applied to flexural waves, where the initial guess of shear slowness is picked from the slowness density map of flexural waves after dispersion-correction processing.
This paper shows a case study of borehole flexural and screw waves processing in soft formations. A modified differential-phase frequency-semblance (MDPFS) approach is applied to extract the mode waves’ full-frequency dispersion response from measured waveforms. The data-driven shear slowness processing is applied to the dispersion response. Both dipole flexural waves and quadrupole screw waves are processed. A combination of slowness density log from the flexural or screw wave slowness and the dispersion-corrected slowness is used as a QC metric of the final estimated shear. Results show that flexural and screw dispersions are well measured by the LWD sonic tool, even if the shear slowness is as large as 500 ms/ft. Shear slowness extracted from flexural waves and screw waves match well with each other and with wireline shear slowness logs, demonstrating that the processing is reliable and robust.
Biography:
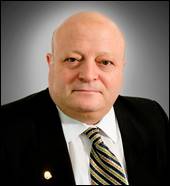